Article by Donaldson Filtration
The production of breathing air is one of the most sensitive tasks in medical and industrial applications. In an environment where respiratory masks and protective suits need to be worn, it is essential to supply employees with clean breathing air that complies with the requirements of DIN EN 12021 and DIN EN ISO 7396-1 and the quality standard of the European Pharmacopoeia. A stationary or mobile compressed air supply is available for applications involving exposure to dust or solvents, such as sandblasting and painting work, long-term refurbishments contaminated with asbestos, and in the chemical and pharmaceutical industries under the influence of gases and contaminated aerosols. This compressed air, generated under a wide range of environmental conditions by compressors of various types, must be processed into breathing air that meets these specifications.
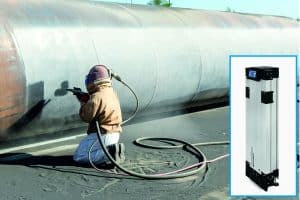
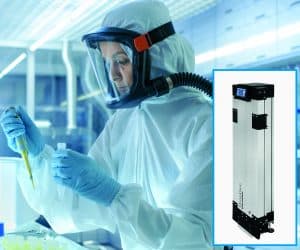
A compact plug & work solution for many applications
It was a complex task to develop a breathing air system that can be used equally flexibly for different areas of application and that reliably ensures the supply of breathing air in accordance with this high-quality standard while requiring little space. Building on the experience gained in the use of the modular, heatless, plug & work, compressed air purification system Ultrapacâ„¢ Smart, Donaldson developed the Ultrapure Smart breathing air system, which sets a new standard through its compact design and easy access to all components. Modularity allows for both vertical and horizontal operation, and the rotatable display can be placed independent from the dryer to easily monitor functions. An advantage for plug & work use: the inlet and outlet connections can be rotated to the position required at the installation site for pipe or hose connections, e.g., with quick-connect couplings. To ensure very quiet operation even in laboratories or medical applications, a silencer specially developed for this dryer range is integrated to reduce the sound level to the 60 dB(A) range.
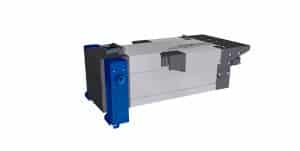
From compressed air to breathing air – flexible, efficient, and reliable
Looking at the process flow from compressed air to breathing air, the high level of development of the components designed for filtration and adsorption is evident. This ensures maximum results in the smallest possible space: the compressed air generated by the compressor is cleaned from condensate and particles in the first stage by an UltraPleatâ„¢ coalescence filter (1), and the condensate is removed via a condensate drain (2).
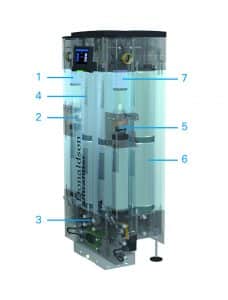
Via a shuttle valve (3), the air is led into the desiccant cartridges (4) in a flow-optimized manner to remove water and CO2. With the preloaded, highly effective desiccant – still fully utilized even in the partial flow – a long service life can be achieved and the desired degree of dryness (pressure dew point max. -40°C at 100% nominal load) is reliably achieved and kept.
In this continuous process – validated to ISO 7183 – adsorption and regeneration take place alternately in the two cartridges. Effective heatless regeneration is achieved by a partial flow of the dried air, so that autonomous use is possible without a separate energy supply. The control system, which is optionally equipped with a dew point transmitter (5), ensures that this process runs according to consumption and automatically switches to energy-saving mode.
In the final purification stage (6) from compressed air to breathing air, traces of CO2, SO2 and NOX are adsorbed, and CO is transformed into CO2 through a catalytic reaction. Oil vapours and hydrocarbons are adsorbed as well as taste and odour molecules. An UltraPleat™ particulate filter (7) ensures that even the last remaining solid particles down to 0.01 µm are removed. The result: ultra-pure breathing air in accordance with international standards.